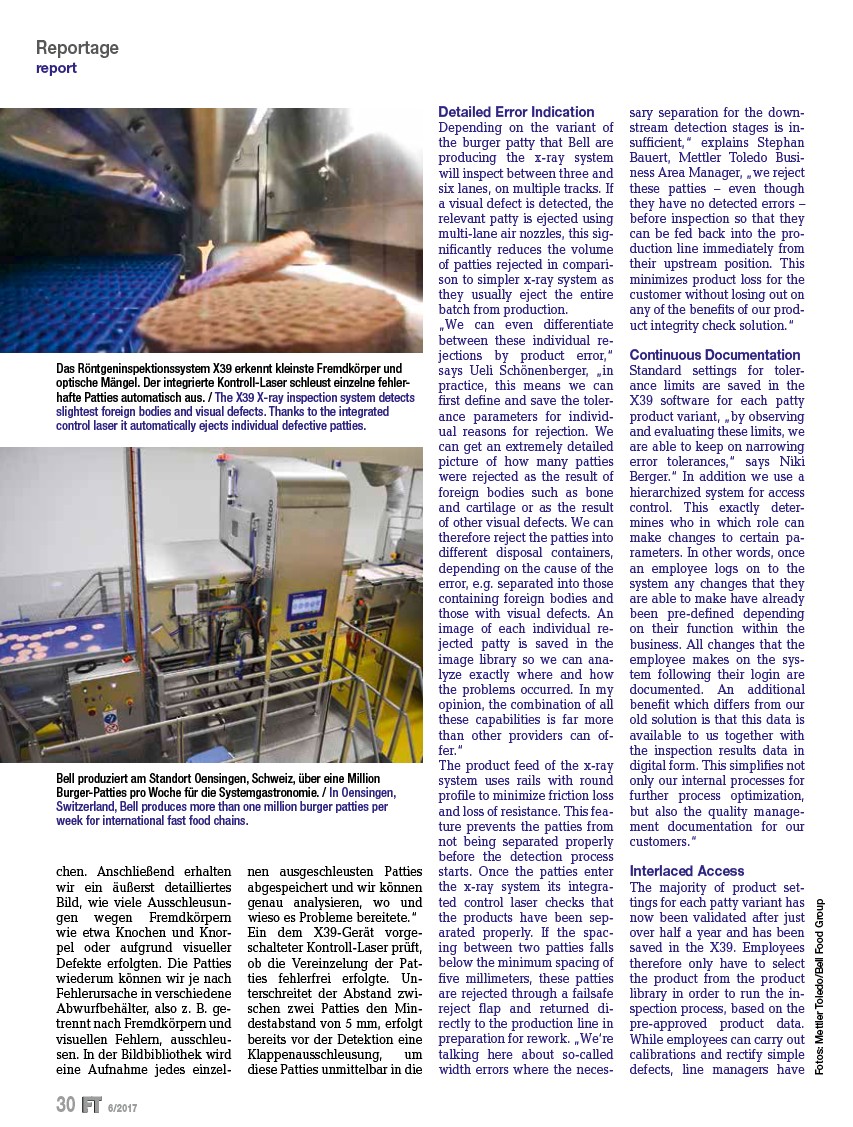
Reportage
report
chen. Anschließend erhalten
wir ein äußerst detailliertes
Bild, wie viele Ausschleusun-gen
wegen Fremdkörpern
wie etwa Knochen und Knor-pel
oder aufgrund visueller
Defekte erfolgten. Die Patties
wiederum können wir je nach
Fehlerursache in verschiedene
Abwurfbehälter, also z. B. ge-trennt
nach Fremdkörpern und
visuellen Fehlern, ausschleu-sen.
In der Bildbibliothek wird
eine Aufnahme jedes einzel-nen
ausgeschleusten Patties
abgespeichert und wir können
genau analysieren, wo und
wieso es Probleme bereitete.“
Ein dem X39-Gerät vorge-schalteter
Kontroll-Laser prüft,
ob die Vereinzelung der Pat-ties
fehlerfrei erfolgte. Un-terschreitet
der Abstand zwi-schen
zwei Patties den Min-destabstand
von 5 mm, erfolgt
bereits vor der Detektion eine
Klappenausschleusung, um
diese Patties unmittelbar in die
Detailed Error Indication
Depending on the variant of
the burger patty that Bell are
producing the x-ray system
will inspect between three and
six lanes, on multiple tracks. If
a visual defect is detected, the
relevant patty is ejected using
multi-lane air nozzles, this sig-nificantly
reduces the volume
of patties rejected in compari-son
to simpler x-ray system as
they usually eject the entire
batch from production.
„We can even differentiate
between these individual re-jections
by product error,“
says Ueli Schönenberger, „in
practice, this means we can
first define and save the toler-ance
parameters for individ-ual
reasons for rejection. We
can get an extremely detailed
picture of how many patties
were rejected as the result of
foreign bodies such as bone
and cartilage or as the result
of other visual defects. We can
therefore reject the patties into
different disposal containers,
depending on the cause of the
error, e.g. separated into those
containing foreign bodies and
those with visual defects. An
image of each individual re-jected
patty is saved in the
image library so we can ana-lyze
exactly where and how
the problems occurred. In my
opinion, the combination of all
these capabilities is far more
than other providers can of-fer.“
The product feed of the x-ray
system uses rails with round
profile to minimize friction loss
and loss of resistance. This fea-ture
prevents the patties from
not being separated properly
before the detection process
starts. Once the patties enter
the x-ray system its integra-
ted control laser checks that
the products have been sep-arated
properly. If the spac-ing
between two patties falls
below the minimum spacing of
five millimeters, these patties
are rejected through a failsafe
reject flap and returned di-rectly
to the production line in
preparation for rework. „We‘re
talking here about so-called
width errors where the neces-sary
separation for the down-stream
detection stages is in-sufficient,“
explains Stephan
Bauert, Mettler Toledo Busi-ness
Area Manager, „we reject
these patties – even though
they have no detected errors –
before inspection so that they
can be fed back into the pro-duction
line immediately from
their upstream position. This
minimizes product loss for the
customer without losing out on
any of the benefits of our prod-uct
integrity check solution.“
Continuous Documentation
Standard settings for toler-ance
limits are saved in the
X39 software for each patty
product variant, „by observing
and evaluating these limits, we
are able to keep on narrowing
error tolerances,“ says Niki
Berger.“ In addition we use a
hierarchized system for access
control. This exactly deter-mines
who in which role can
make changes to certain pa-rameters.
In other words, once
an employee logs on to the
system any changes that they
are able to make have already
been pre-defined depending
on their function within the
business. All changes that the
employee makes on the sys-tem
following their login are
documented. An additional
benefit which differs from our
old solution is that this data is
available to us together with
the inspection results data in
digital form. This simplifies not
only our internal processes for
further process optimization,
but also the quality manage-ment
documentation for our
customers.“
Interlaced Access
The majority of product set-tings
for each patty variant has
now been validated after just
over half a year and has been
saved in the X39. Employees
therefore only have to select
the product from the product
library in order to run the in-spection
process, based on the
pre-approved product data.
While employees can carry out
calibrations and rectify simple
defects, line managers have
Das Röntgeninspektionssystem X39 erkennt kleinste Fremdkörper und
optische Mängel. Der integrierte Kontroll-Laser schleust einzelne fehler-hafte
Patties automatisch aus. / The X39 X-ray inspection system detects
slightest foreign bodies and visual defects. Thanks to the integrated
control laser it automatically ejects individual defective patties.
Bell produziert am Standort Oensingen, Schweiz, über eine Million
Burger-Patties pro Woche für die Systemgastronomie. / In Oensingen,
Switzerland, Bell produces more than one million burger patties per
week for international fast food chains.
30 6/2017
Fotos: Mettler Toledo/Bell Food Group